In the dynamic realm of powder coating, the
Powder Coat Line serves as a pivotal asset for industries striving to attain top - tier coating outcomes. This article will comprehensively explore every aspect of this indispensable equipment.
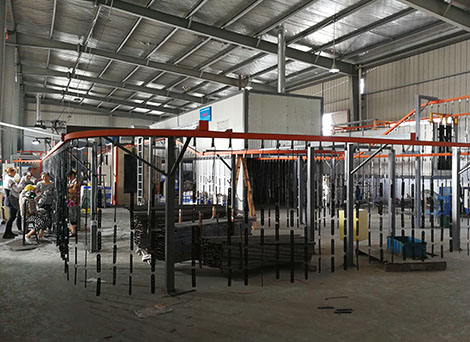
A
Powder Coat Line is an integrated system engineered to streamline the powder coating process. It typically comprises multiple interconnected components:
Pre - treatment Section: This marks the starting point of the line. It cleans and readies the workpiece surface. Common pre - treatment methods encompass degreasing to eliminate oil and grease, phosphating to boost paint adhesion, and sandblasting to create a rough surface for enhanced powder grip.
Powder - Spraying Booth: Here, the powder is applied to the workpiece. The booth is equipped with powder - spraying guns, which can be manual or automated. Automated guns are frequently employed in high - volume production to ensure consistent results. The booth also features a ventilation system to remove over - sprayed powder and uphold a safe working environment.
Curing Oven: Subsequent to powder application, the workpiece enters the curing oven. The oven heats the powder - coated workpiece to a specific temperature, melting and fusing the powder to form a durable finish. It can be electrically or gas - fired, and usually has precise temperature - control mechanisms.
Conveyor System: This system transports the workpiece through each stage of the powder coat line. It ensures a continuous and efficient production process, with adjustable speeds to accommodate diverse production requirements.
Automotive Industry: Utilized for coating car bodies, engine parts, and wheels. The powder coating offers excellent corrosion resistance and a sleek appearance, enhancing the vehicle's overall quality.
Furniture Manufacturing: Metal furniture frames, legs, and decorative elements are coated to improve their aesthetics and durability. The powder coating can mimic the appearance of various materials, adding versatility to furniture designs.
Construction Industry: Applied to metal building components such as window frames, handrails, and roofing materials. The powder coating safeguards these components from the elements, extending their lifespan.
Electrical Appliance Manufacturing:
Powder Coat Lines are used to coat the outer shells of appliances like refrigerators, washing machines, and air conditioners, providing protection and an appealing finish.
The price of a
Powder Coat Line can vary significantly depending on its complexity and features:
Basic Powder Coat Line: For small - scale workshops or hobbyists, a basic line with simple pre - treatment, a manual powder - spraying booth, and a small curing oven can cost approximately $20,000 - $50,000.
Mid - Range Powder Coat Line: A mid - range line, featuring higher - quality components, semi - automated powder - spraying, and a more efficient curing oven, may cost between $50,000 - $150,000. This type of line is suitable for medium - sized production facilities.
High - End Industrial Powder Coat Line: High - end lines, equipped with advanced pre - treatment systems, fully automated powder - spraying, and large - capacity curing ovens, can cost upwards of $150,000. These are designed for large - scale manufacturing plants with high - volume production needs.
Pre - operation Setup: Prior to starting the line, ensure all components are properly installed and calibrated. Prime the pre - treatment chemicals as per the instructions. Check the powder - spraying guns and adjust the powder - flow rate and electrostatic voltage as required. Pre - heat the curing oven to the requisite temperature.
Operation: Initiate the conveyor system at an appropriate speed. As the workpiece moves through the pre - treatment section, ensure the treatment is effective. In the powder - spraying booth, maintain an appropriate distance between the gun and the workpiece (usually 15 - 20 cm) and move the gun steadily for an even coating. In the curing oven, adhere to the recommended curing time and temperature for the specific powder being used.
Post - operation Maintenance: After use, clean the powder - spraying guns, powder - reclaim system, and the curing oven. Check for any signs of wear or damage in all components and replace parts if necessary.
Production Volume: Consider your current and future production volume. High - volume production necessitates a fully automated, high - end powder coat line. For small - scale production, a basic or mid - range line will suffice.
Workpiece Types: Different workpiece shapes and sizes may demand specific features in the powder coat line. For instance, complex - shaped workpieces may require more flexible powder - spraying options.
Budget: Set a realistic budget based on your financial capabilities and business needs. Bear in mind that investing in a higher - quality line may lead to better - quality coatings and lower long - term costs.
Supplier Reputation: Choose a supplier with a good reputation for quality equipment, reliable after - sales service, and technical support.
Personal Protective Equipment (PPE): Workers should don appropriate PPE, including safety glasses, masks, and gloves, to safeguard against powder inhalation, splashes, and potential burns.
Ventilation: Ensure proper ventilation in the powder - spraying area to prevent the accumulation of powder dust, which can pose a fire or explosion hazard.
Electrical Safety: Regularly inspect the electrical components of the line, including the curing oven and conveyor system, to prevent electrical accidents.
Fire Prevention: Keep flammable materials away from the powder coat line. Install fire - extinguishing equipment and have a fire - prevention plan in place.
Efficiency: The conveyor - based system enables continuous production, augmenting productivity. The separation of pre - treatment, powder - spraying, and curing stages ensures that each process is optimized.
Quality Control: Precise temperature control in the curing oven and adjustable powder - spraying parameters enable high - quality and consistent coatings.
Cost - effectiveness: The ability to recycle over - sprayed powder and the long - lasting nature of powder coatings reduce material and maintenance costs over time.
Q: What should I do if the powder coating has an uneven thickness?
A: Check the powder - spraying parameters, such as powder - flow rate and electrostatic voltage. Ensure the gun movement is steady and the conveyor speed is consistent. Also, verify that the workpiece surface is clean and properly pre - treated.
Q: Can I customize the powder coat line according to my production needs?
A: Most suppliers offer customization options. You can discuss your specific requirements, such as production volume, workpiece size, and coating quality standards, with the supplier.
Q: How often should I maintain the curing oven?
A: Conduct a monthly inspection of the heating elements, temperature sensors, and insulation. Perform a comprehensive maintenance every 3 - 6 months, including cleaning, calibration, and replacement of worn - out parts.
Q: What if the powder - spraying booth has a powder leakage problem?
A: Check the seals of the booth and the powder - reclaim system. Replace any damaged seals and ensure all doors and access points are properly closed. Also, check for blockages in the powder - reclaim ducts.
Q: Can I use different types of powder coatings on the same powder coat line?
A: Yes, but you need to clean the powder - spraying and powder - feeding systems thoroughly between different powder types to avoid contamination.
Disclaimer: Enhance your coating process with advanced electrostatic powder coating machines, precision powder coating spray guns, comprehensive powder coating systems, and efficient powder coating lines from Hangzhou Huaxiang Coating Equipment Co., Ltd. Designed for reliability and high-quality finishes, our solutions meet all your industrial powder coating machine needs. Contact us at sale3@cncolourspray.com